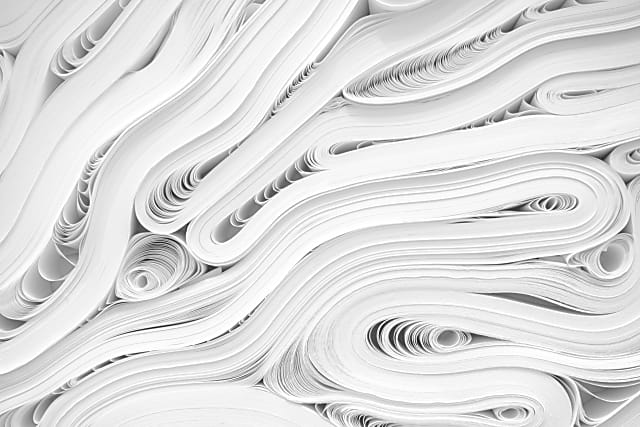
White papers
Stay up to date on the latest topics and gain industry insights from HMS' experts through our white papers, providing valuable knowledge and analysis.
The Ewon Cosy VPN gateway simplifies remote access, streamlining the process and improving efficiency in commissioning and maintenance for the Egan IntelliBatch systems in the concrete industry.
Commissioning costs for OEMs have always been extra costs that are borne by the customer. Depending on the complexity of the machine and its integration with other peripheral equipment, commissioning could take days to weeks (sometimes months) installing, integrating, and training end users on how to use the equipment. In the past, the location of the systems integrator for the equipment could be the difference between the success and failure of machinery. With the advent of Ethernet communication across a wide area network (WAN), more OEMs use a Virtual Private Network (VPN) to lower commissioning costs, allow an expert to virtually assist a distributor or local installers process.
As a next step, the Ewon Cosy makes remote access significantly easier to obtain, foregoing the need for a traditional VPN, allowing facilities IT departments to simply connect an Ethernet cable, making the facilities IT infrastructure more secure, lowering an End Users cost of ownership, and decreasing commissioning and troubleshooting effort by the customer.
During the pandemic, we’ve seen service costs significantly decreased by implementing the Ewon Cosy, especially during the commissioning process. Customers now assume commissioning can be done remotely.
Dan Loney, Product and OEM Engineering Manager, Egan
Egan Company based out of Champlin, Minnesota is a premier contractor and single source trades provider that specializing in a multitude of skilled trades and professional services which include a process controls system integration division. This division of Egan Company has created IntelliBatch concrete batching solution. This control system is used in Precast, Block and Paver, and Bagging Concrete plants globally. The IntelliBatch solution allows customers to support multiple mix batches on multiple machine platforms with an easy to use interface. IntelliBatch allows customer’s customization of timing and control logic, creating high quality production value.
These IntelliBatch systems are typically housed at customer sites, which means that the commissioning and troubleshooting are all remote to Egan. Dan Loney is the Product and OEM Engineering Manager at Egan “The Concrete market is seasonal, from a busy commissioning period in Spring, to a very slow non-active period in Summer. This makes timelines significantly tight during the spring”. Prior to using Ewon, troubleshooting would happen over the phone, occasionally through VPN and sometimes travel to the site was necessary. Most customers do not have a dedicated IT person or team at their facility. The customers that do usually have VPN connectivity issues, which cost an average of 4 hours of overhead time. Having to remotely connect to any controller and automation equipment Egan offers can take significant time as well, as each controller may have different VPN requirements. Commissioning costs are difficult, requiring an engineer travel on site with a limited time frame.
Having an easy-to-use remote access tool allowed service costs during troubleshooting and commissioning to be lessened considerably. Instead of having multiple dedicated controls engineers per machine, they can use a few senior controls engineers for all North American installations, significantly reducing labor costs. Says Dan, “During the Pandemic, we’ve seen service costs significantly decreased, especially during the commissioning process. Customers now assume commissioning can be done remotely.” The entire troubleshooting session now costs around 1 hour. The Ewon Cosy can connect to any PLC used, including legacy systems from Rockwell and Siemens. It eliminates the need to call IT other than to simply ask “ do you have an internet connection? ”.
In addition, training new engineers has been lowered due to the ability to connect and assist easily, all they need is a cell phone to connect to the Wi-Fi Cosy. A Senior Engineer can be remotely connected in and show the Junior Engineer the steps necessary to properly commission an Intellibatch system. Users also can benefit from an Email and Mobile Alert system, which shows Facility managers and Egan any down time or alarms have been seen recently. Egan can then move from a reactive to a proactive service team, increasing customer satisfaction and decreasing total cost of ownership.
Stay up to date on the latest topics and gain industry insights from HMS' experts through our white papers, providing valuable knowledge and analysis.
Our products solve everyday industrial communication problems. Discover how our customers have improved their business with HMS case studies.
HMS communication solutions help thousands of companies solve specific communication problems in many different industries and applications.