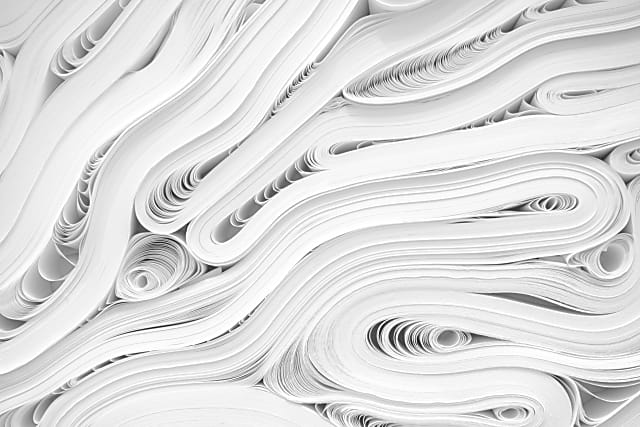
White papers
Stay up to date on the latest topics and gain industry insights from HMS' experts through our white papers, providing valuable knowledge and analysis.
Ixxat CANblue II connects CAN network of test vehicle ECU via Bluetooth with tablet PCs and makes driving tests more "tangible" by displaying vehicle data.
Schaeffler Engineering has been developing demo car projects for many years in order to demonstrate the performance of its products in the field of electromobility on “living objects“.
In some projects it’s useful to pick up certain vehicle data – which are available at central control units (ECU) of the in-vehicle network (IVN) in CAN (Controller Area Network) format – and make them available for the respective test driver.
Since the “temporary” wiring of electrical equipment in vehicles is difficult to impossible for test purposes, it was not possible to visualize the vehicle‘s information – adapted powertrain and energy flow – sent from Schaeffler’s control unit. As a result, the test drivers had no real-time knowledge of the vehicle‘s operating status.
To improve the situation, Schaeffler Engineering was looking for a solution to connect the CAN network of a vehicle with a display in the driver‘s cab. At first, no suitable solution could be found until Mr. CHEN Xin - Software Manager of Schaeffler Engineering China - became aware of Ixxat‘s versatile CANblue II interface.
Comprising a plug-and-play unit Ixxat CANblue II is a pre-configured CAN-to-Bluetooth bridge that minimizes setup time providing a rapid way of exchanging data of CAN networks with computers, tablet PCs or even Smartphones via Bluetooth. The product supports CAN networks with 11-bit and 29-bit identifiers and facilitates the job of system integrators in situations that make wired connections unsuitable or challenging.
CANblue II connects the CAN network of a testvehicle ECU via Bluetooth with Smartphones or Tablet PCs.
The CANblue II is installed near the drive train of the test vehicles and connected to the vehicle controller via its CAN network interface. Via the the Bluetooth connection of the CANblue II the controller data is transmitted to a tablet PC located in the passenger compartment. The test drivers thereby receive direct, visualized feedback of the vehicle data (e.g. operating status of the electric drive train) and get a vivid impression of the improvements the Schaeffler engineers achieved in the test vehicles.
Fixed wiring of electronic/ electrical components is the “normal” approach, but in some cases difficult to implement. Ixxat CANblue II helped us avoiding permanent wiring, which is almost impossible in our vehicle test situations.
Mr. CHEN Xin, Software Manager, Schaeffler Engineering China
One of the main reasons for the customer to choose CANblue II was the availability of an Android ADK, which makes it possible, among other things, to easily develop a visualization for Tablet PCs. Another main reason was the fact that CANblue II is easy to configure and operate and maintains a stable communication.
Employing a proprietary 2,4 GHz radio and frequency hopping mechanism CANblue II let customers control the data rate and radio packet format and choose either “Shortest Latency“, “Most-Robust Connection“, “Quickest Connection“ or “Default policies“ to achieve predictable latencies, without sacrificing stability or range. This makes CANblue II effective in CAN network infrastructure and control applications, where accurate message delivery times are essential. Transmission range is at least 200 m, with a CAN transmission rate of 100 % bus load at 1 Mbit and a Bluetooth transfer delay which in average is approx. 4 ms for CAN to Bluetooth.
The device comes in two variants, either with internal antenna (11 dBm) or external antenna (13 dBm). Both models share the same functionality but in case of an external antenna customer can choose from a 90 degree tiltable stub antenna, a magnetic foot antenna or a screwable antenna foot.
CANblue II is compliant with CE, FCC and the RoHs Directive 2002/95/EC. The device uses a module which supports Bluetooth® classic (v4.0) with an output frequency of 2.402 to 2.480 GHz (ISM band) and complies with the Japanese Technical Regulation Conformity Certification of Specified Radio Equipment.
The Schaeffler Group is a globally active automotive and industrial supplier. With high-precision components and systems for engine, transmission and chassis applications as well as rolling bearing and plain bearing solutions for a wide range of industrial applications, the Schaeffler Group is already playing a key role in shaping “mobility for tomorrow“ today. As one of the world‘s largest family companies, Schaeffler employs around 89,400 people around the world and is represented at 170 locations in over 50 countries.
Schaeffler Engineering has been part of the Schaeffler Group for more than 15 years and offers a wide range of services with its Engineering Solutions, Powertrain Validation and Products divisions.
Company: Schaeffler Engineering
Country: China
Solution: Ixxat bridges and gateways
Industries: Automotive
Products: Ixxat CANblue II
Stay up to date on the latest topics and gain industry insights from HMS' experts through our white papers, providing valuable knowledge and analysis.
Our products solve everyday industrial communication problems. Discover how our customers have improved their business with HMS case studies.
HMS communication solutions help thousands of companies solve specific communication problems in many different industries and applications.