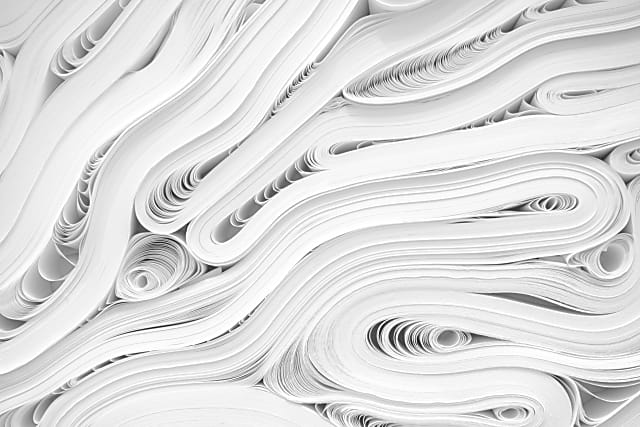
White papers
Stay up to date on the latest topics and gain industry insights from HMS' experts through our white papers, providing valuable knowledge and analysis.
How Speeding Scientists Siegen get CAN diagnostics from their racing car wirelessly at each pit stop.
Since the start in the U.S. in 1981, “Formula Student” has grown to become an international phenomenon with car races all over the world. With donations and sponsorships from companies and institutions, university students build their own racing car from scratch and handle everything from electronic and mechanical engineering to sales and marketing (not to mention the driving itself).
Formula Student is just as much about the learning experience of building a racing car as it is about the actual race, and the teams are awarded not only for the fastest car, but also for the best construction, performance, marketing and sales presentations as well as financial planning.
The University of Siegen in Central Germany has been racing in Formula Student since 2009. About 30-40 students devote their extracurricular time to the project every year and in 2011, they presented their first electric-powered racing car. Building a racing car is an impressive engineering feat, especially since most parts are completely developed by the students and only a few components are off-the-shelf products.
The car’s performance speaks for itself: The 2013 racing car from the University of Siegen is powered by two water-cooled three-phase synchronous servo motors. The car weighs in at 218 kilos, has a max speed of 115 km/h, and the impressive torque of 1040 Nm enables the car to go from 0-100 km/h in 2.9 seconds. The electronic system inside the car uses a CAN-based network controlled by a PLC from Beckhoff.
It has certainly helped our racing team to get quicker and easier diagnostics.
Thilo Becker, Project Engineer Hardware, Speeding Scientists Siegen
The cars have to go through rigorous testing before, during and after the race. To get the diagnostics from the CAN-based electrical systems in the car, The Speeding Scientists found the Ixxat USB to CAN product. With this tool, they were able to get data about the performance of the frequency inverter, the water pumps and the other electrical components inside the car at each pit stop. “We really liked the fact that we could get direct and easy hardware access to the CAN-bus, our self-developed Master Control Board and our Data Acquisition Unit. There was no need for taking a complicated detour via the PLC anymore,” says Thilo Becker, responsible for the electronic data acquisition from the car.
However, one problem still remained: Every time the car had to make a pit stop, the electronics team had to open the car and plug in a wire to acquire the data from the car. This meant that they risked getting in the way of the service team, catering for the mechanical maintenance of the car.
“We wanted to find a way to get the CAN data from the car without plugging in a wire,” says Thilo Becker. “Since we were already successfully using some Ixxat solutions, I found their CANBlue II which would enable wireless CAN communication to get data via Bluetooth every time the car comes into the pit stop.”
Consequently, Thilo Becker and his team of three electronic engineers started looking into designing in the CANBlue II into the race car.
“It was actually quite easy to get going,” he says. “I only had to configure the Ixxat VCI-driver to check for our CANblue II and could directly use our existing software we used before with an Ixxat USB to CAN without any changes. Building up an application accessing CAN via the Ixxat VCI was also done quite easily – I only had a look at the example C# code provided with the VCI installation and easily adjusted this into a solution that worked for us. When the car comes into the pit stop, we get a quick overview of how all the systems are functioning and with a few clicks of the mouse, we can set and reset any fuses in the car, enabling it to get back in the race. More importantly, we can do all this from a distance without getting in the way of the service team checking tires and the more mechanical aspects of the car.”
But turning to a wireless CAN communication solution also meant other challenges for the racing team. Firstly, they had to find a solution that could cope with the EMI emissions of the powerful electric engine – especially since the CANBlue II had to be placed close to the engine. Another challenge was to get a strong enough Bluetooth signal to penetrate the bodywork, made from a carbon fiber and copper mesh.
The team – Speeding Scientists Siegen
“The EMI turned out to be less of a problem than we first feared, and the CANblue worked just fine despite the interference” says Thilo Becker. “The copper mesh in the bodywork did weaken the signal as expected, but since we are always between 2-10 meters from the car in the pit stop, we can still get a strong enough signal to get the diagnostics from the car. For the next generation of the car, we will use the CANBlue II with an external antenna which will solve this issue as the antenna can be placed on the outside of bodywork.”
All in all, the CANBlue II has been a welcome addition to the Speeding Scientists Siegen racing team enabling them to get quick and easy CAN diagnostics without physically accessing the car. “We are able to get data faster and easier than before and it has certainly helped our racing team to get quicker and easier diagnostics,” concludes Thilo Becker.
Company: Speeding Scientists Siegen
Country: Germany
Solution: Ixxat PC interfaces
Industries: Automotive testing
Products: Ixxat CANblue II
Stay up to date on the latest topics and gain industry insights from HMS' experts through our white papers, providing valuable knowledge and analysis.
Our products solve everyday industrial communication problems. Discover how our customers have improved their business with HMS case studies.
HMS communication solutions help thousands of companies solve specific communication problems in many different industries and applications.